Titanium (Ti): Discovery, Properties, and Applications
Titanium, denoted by the chemical symbol Ti, is an element widely known for its remarkable properties and versatile applications across various industries. From aerospace engineering to biomedical implants, titanium has left a significant imprint on modern technology. This comprehensive guide will delve into its discovery, position in the periodic table, scientific characteristics, and notable technological applications.
The Discovery of Titanium
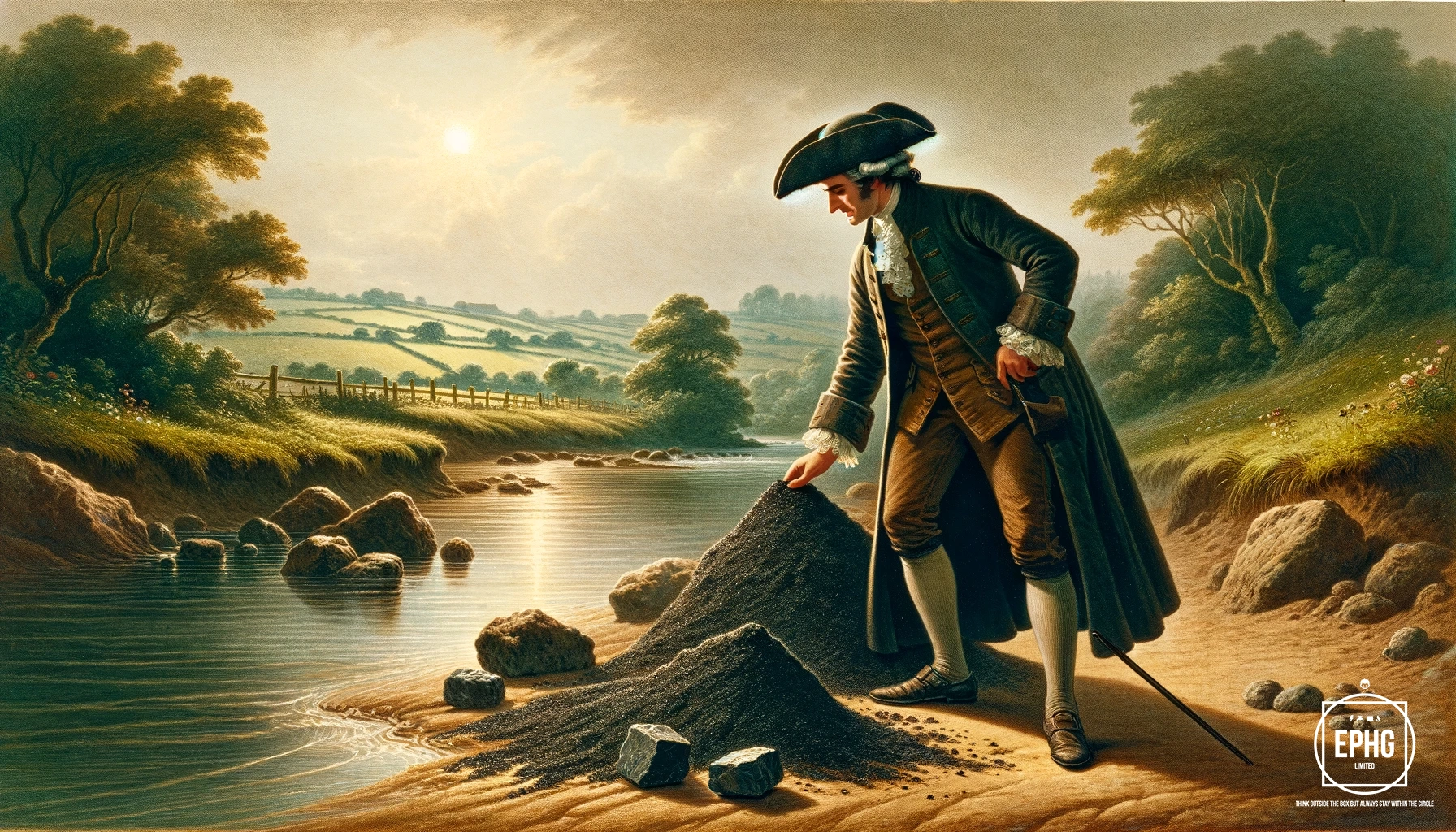
Titanium was first discovered in 1791 by William Gregor, an English clergyman and amateur geologist. While analyzing ilmenite, a mineral obtained from the banks of a stream in Cornwall, he observed a new metal oxide that contained a previously unidentified element. He named the oxide "manaccanite," after the village of Manaccan where it was found. A few years later, in 1795, German chemist Martin Heinrich Klaproth independently identified the same metal and named it "titanium," inspired by the Titans of Greek mythology.
Pure Titanium and Its Characteristics
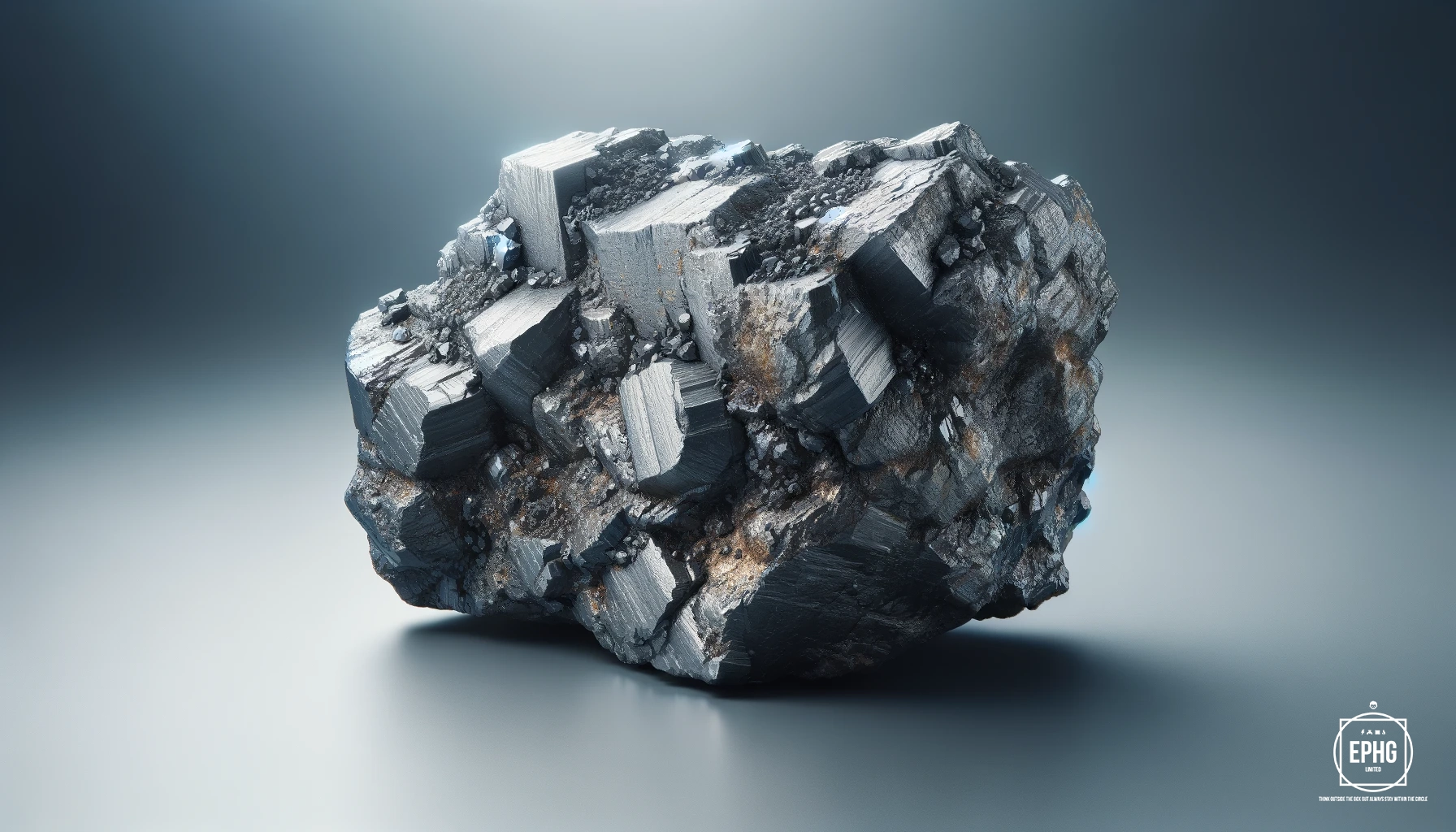
Pure titanium, often referred to as titanium grade 1, is the most ductile and softest form of this element, showcasing the highest degree of formability. Known for its exceptional corrosion resistance, pure titanium is almost entirely resistant to corrosion in aqueous environments, which makes it highly valuable for maritime and aviation applications. Its natural oxide layer shields the metal from a variety of aggressive substances. Pure titanium is also remarkably biocompatible, leading to its widespread use in medical implants such as joint replacements and dental devices. Furthermore, it has a relatively low thermal and electrical conductivity compared to other metals, which adds unique advantages in specific industrial applications. Despite its strength, titanium’s light weight makes it an excellent choice for applications that benefit from high strength-to-weight ratios, such as in aerospace and automotive designs.
Position of Titanium in the Periodic Table
Titanium is the 22nd element in the periodic table, with an atomic number of 22 and an atomic weight of 47.867. It belongs to the group of transition metals and is positioned in group 4, period 4. Transition metals are characterized by their ability to form various oxidation states and create colorful compounds. Titanium's electron configuration, [Ar] 3d² 4s², contributes to its unique chemical and physical properties.
Scientific Properties of Titanium
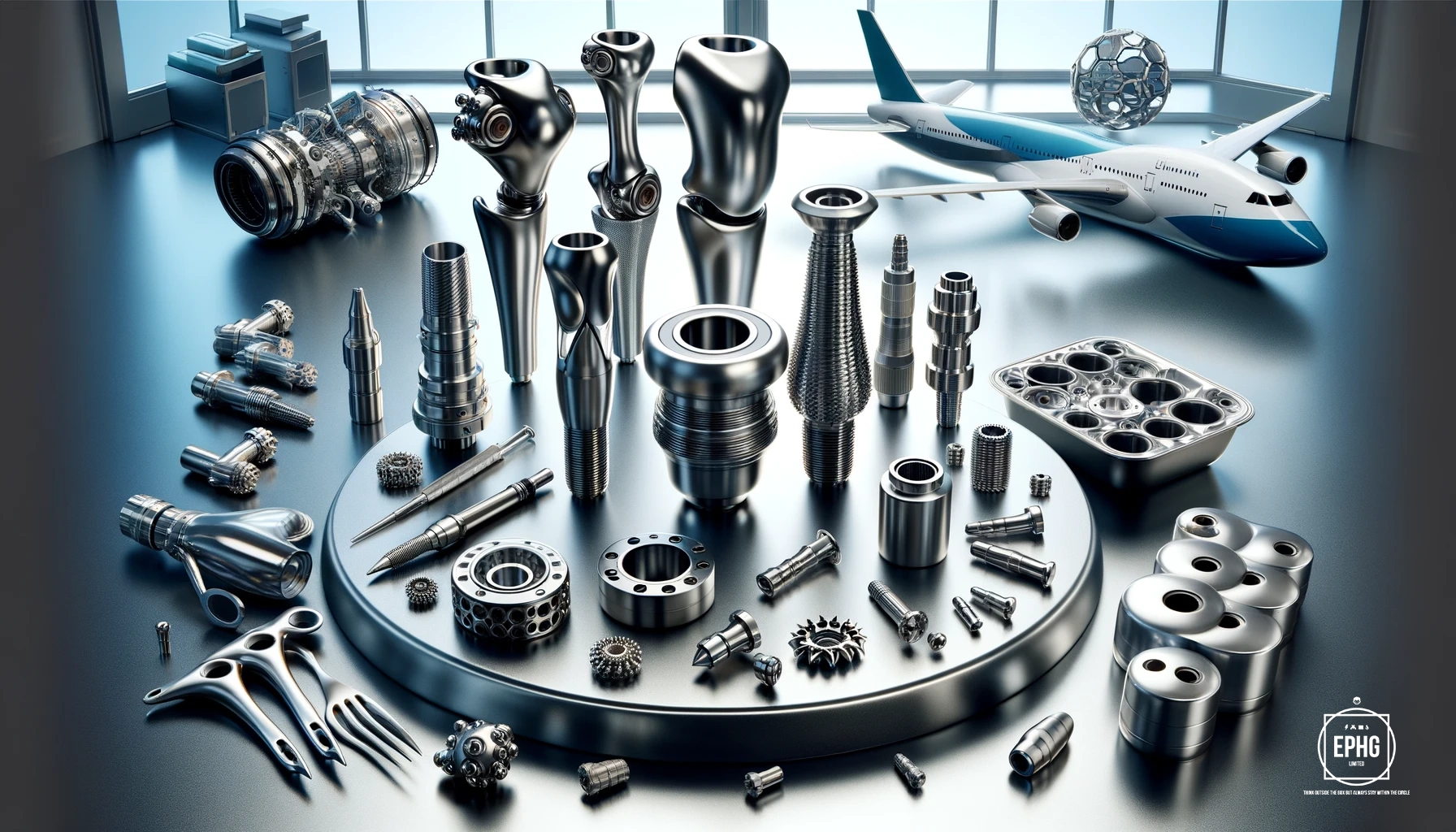
Titanium stands out among the elements due to its unique combination of properties:
- Strength and Low Density: Titanium is known for its exceptional strength-to-weight ratio. It is as strong as steel but only 45% as dense, making it an ideal material where weight reduction is crucial.
- Corrosion Resistance: A thin, stable oxide layer forms on titanium's surface, providing it with excellent resistance to corrosion from seawater, acids, and other harsh environments.
- Biocompatibility: Titanium is non-toxic and biocompatible, meaning it is safe to use in the human body, making it suitable for medical implants and prosthetics.
- High Melting Point: Titanium has a high melting point of approximately 1,668 °C (3,034 °F), making it suitable for high-temperature applications.
- Non-Magnetic: Titanium is non-magnetic, which makes it ideal for use in sensitive equipment where magnetic interference could be problematic.
- Heat Transfer: Though not as conductive as copper or aluminum, titanium's thermal conductivity is adequate for many engineering applications.
Applications of Titanium in Technology
Thanks to these advantageous properties, titanium is used in a wide range of technologies and industries:
Aerospace Engineering with Titanium
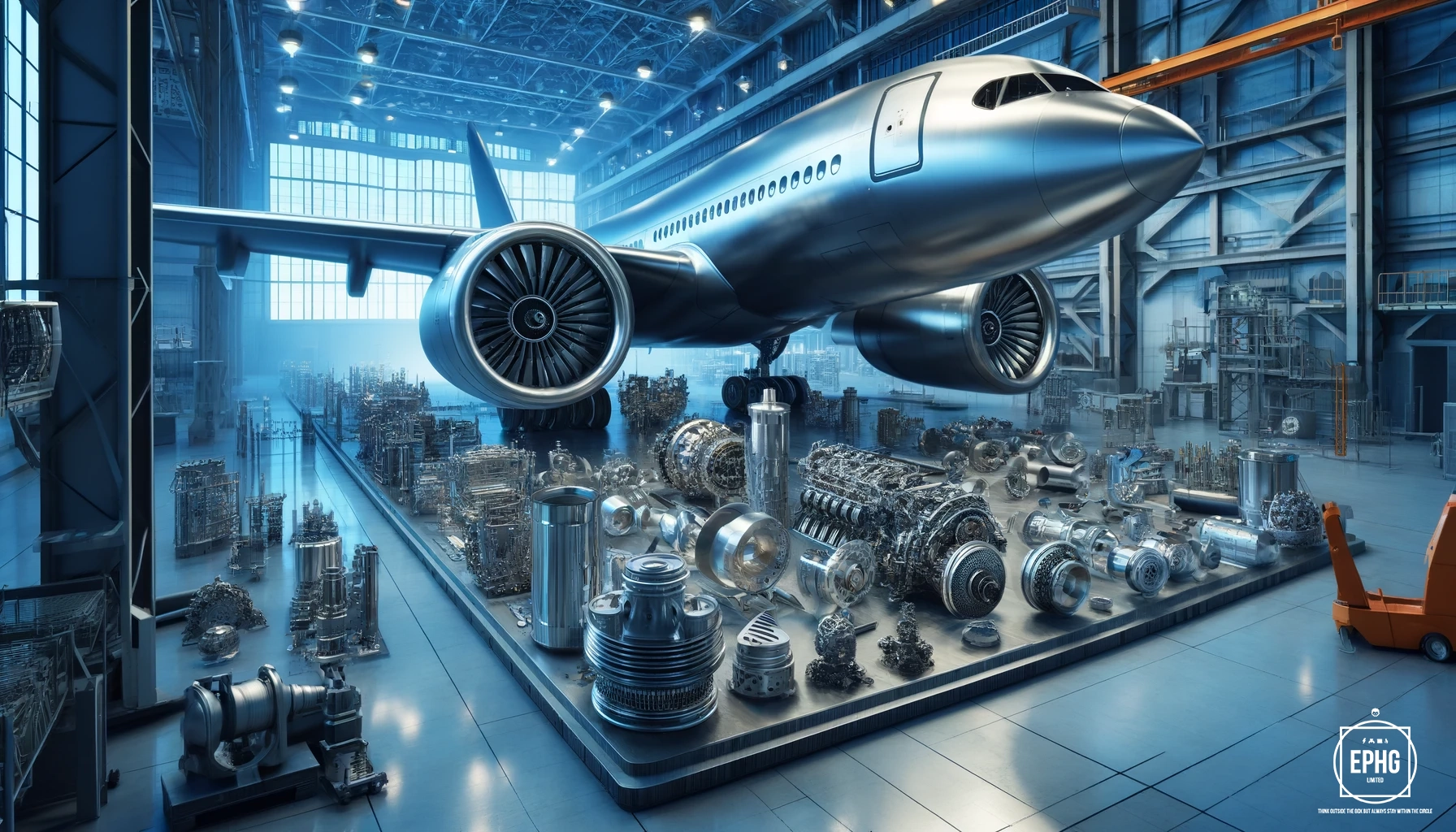
Titanium is a staple in the aerospace industry due to its excellent strength-to-weight ratio and resistance to corrosion. Aircraft components like jet engines, landing gear, and airframe structures extensively utilize titanium alloys. The metal’s resistance to extreme temperatures makes it perfect for applications in aircraft engines that demand high thermal stability. Titanium is also used in space exploration, ensuring spacecraft can withstand the harsh conditions of outer space.
Medical and Biomedical Applications of Titanium
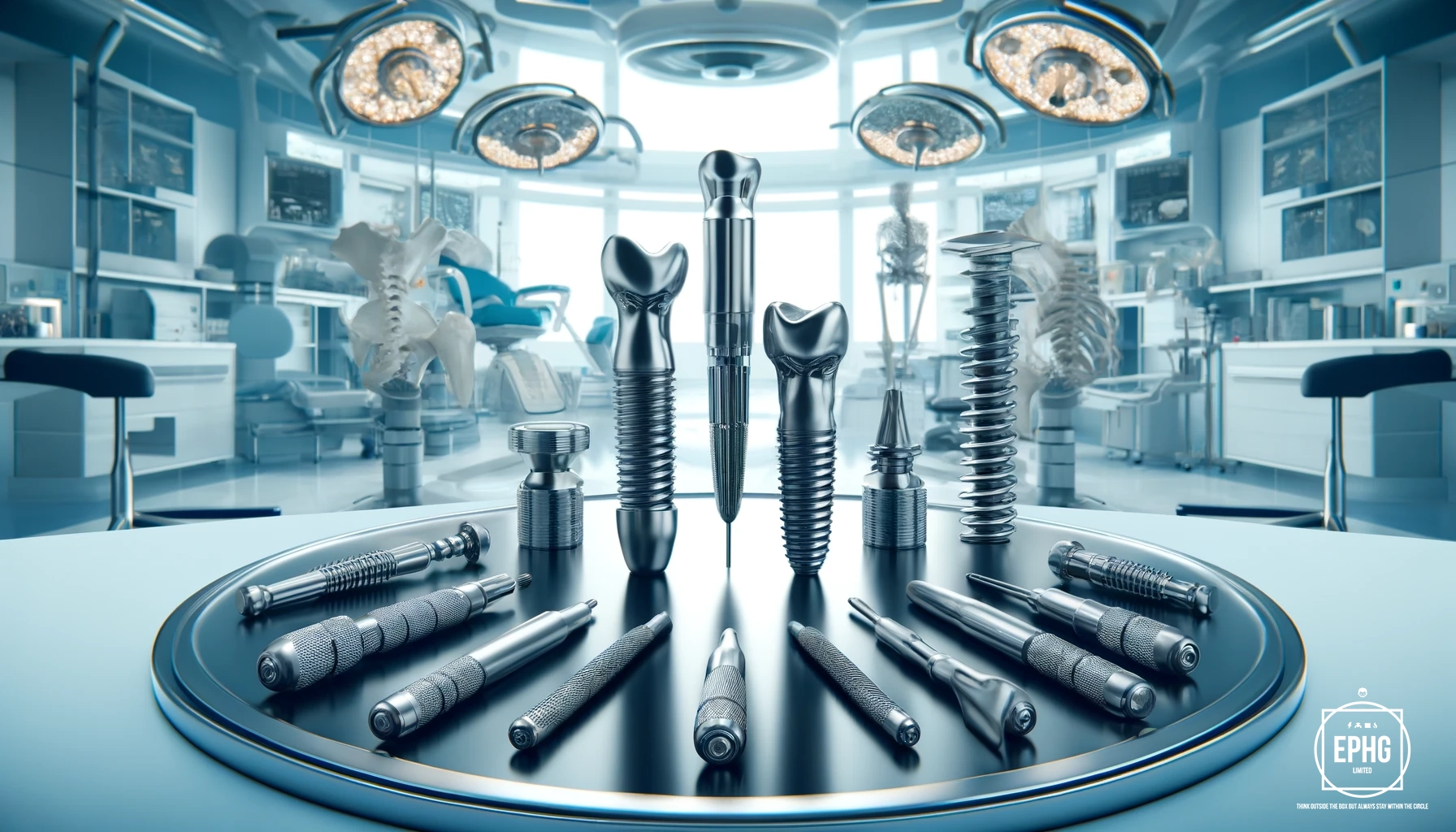
Titanium's exceptional biocompatibility and resistance to corrosion have made it a highly favored material in the biomedical field. It is commonly employed in the creation of dental implants, orthopedic implants (such as hip and knee replacements), and is extensively used in craniofacial reconstructive surgeries. Due to titanium’s outstanding ability to integrate with bone tissue, known as osseointegration, medical professionals are able to design and create durable, long-lasting prosthetics that significantly enhance the quality of life for patients. Moreover, titanium’s inertness makes it an ideal choice for these applications, as it does not react adversely with body tissues, ensuring safety and comfort for long-term implantation.
Marine Engineering with Titanium
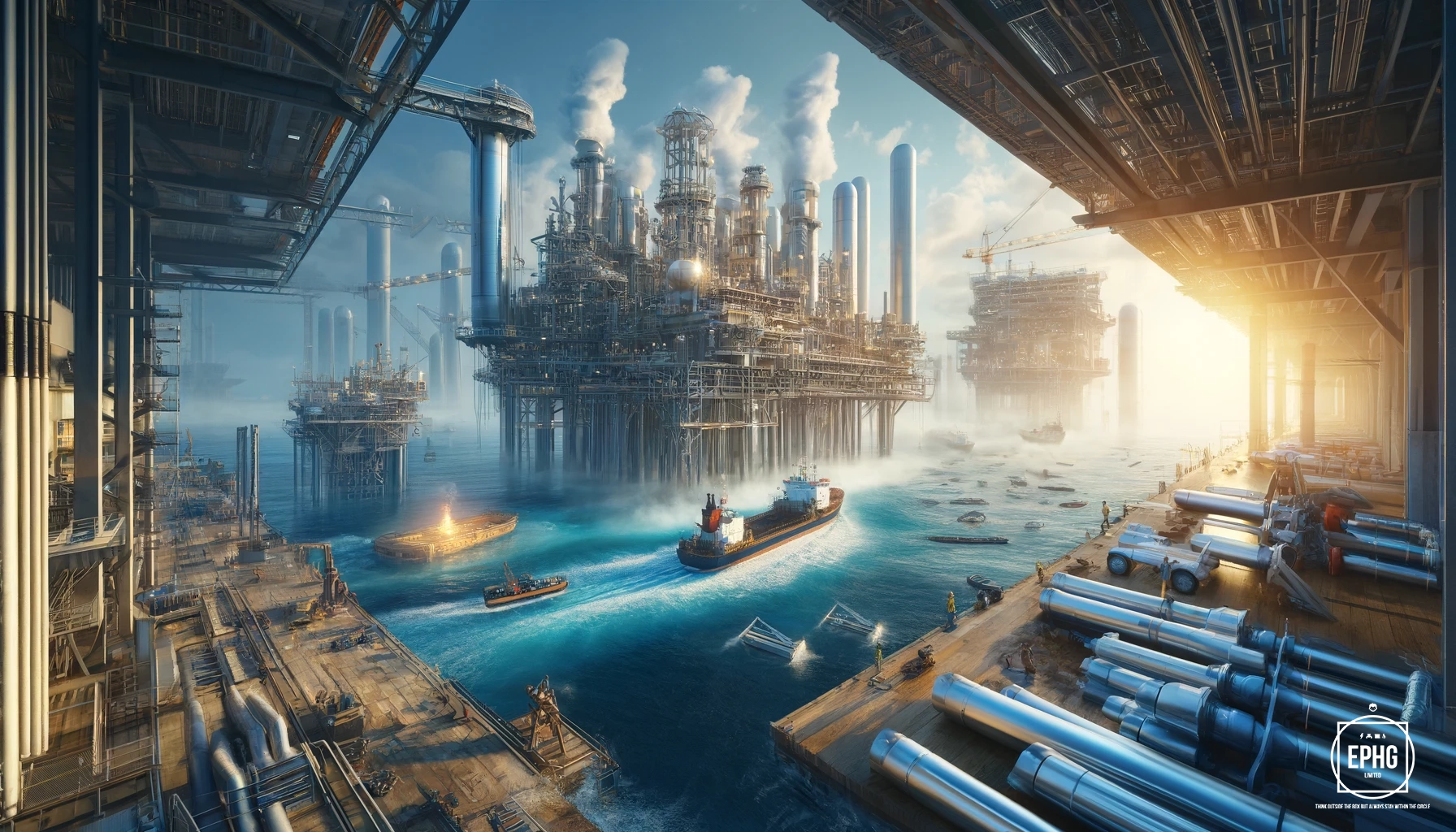
Due to its excellent resistance to seawater corrosion, titanium is widely used in various marine environments. It finds critical applications in shipbuilding, offshore oil and gas production, and desalination plants, among others. For instance, titanium is extensively utilized in heat exchangers and condenser tubing systems due to its superior longevity and exceptional resistance to pitting, crevice corrosion, and biofouling. Additionally, the strength and lightweight nature of titanium allow for more efficient designs in marine structures, further enhancing their operational life and reducing maintenance needs. This makes titanium an invaluable resource in harsh oceanic conditions.
Automotive Industry and Titanium
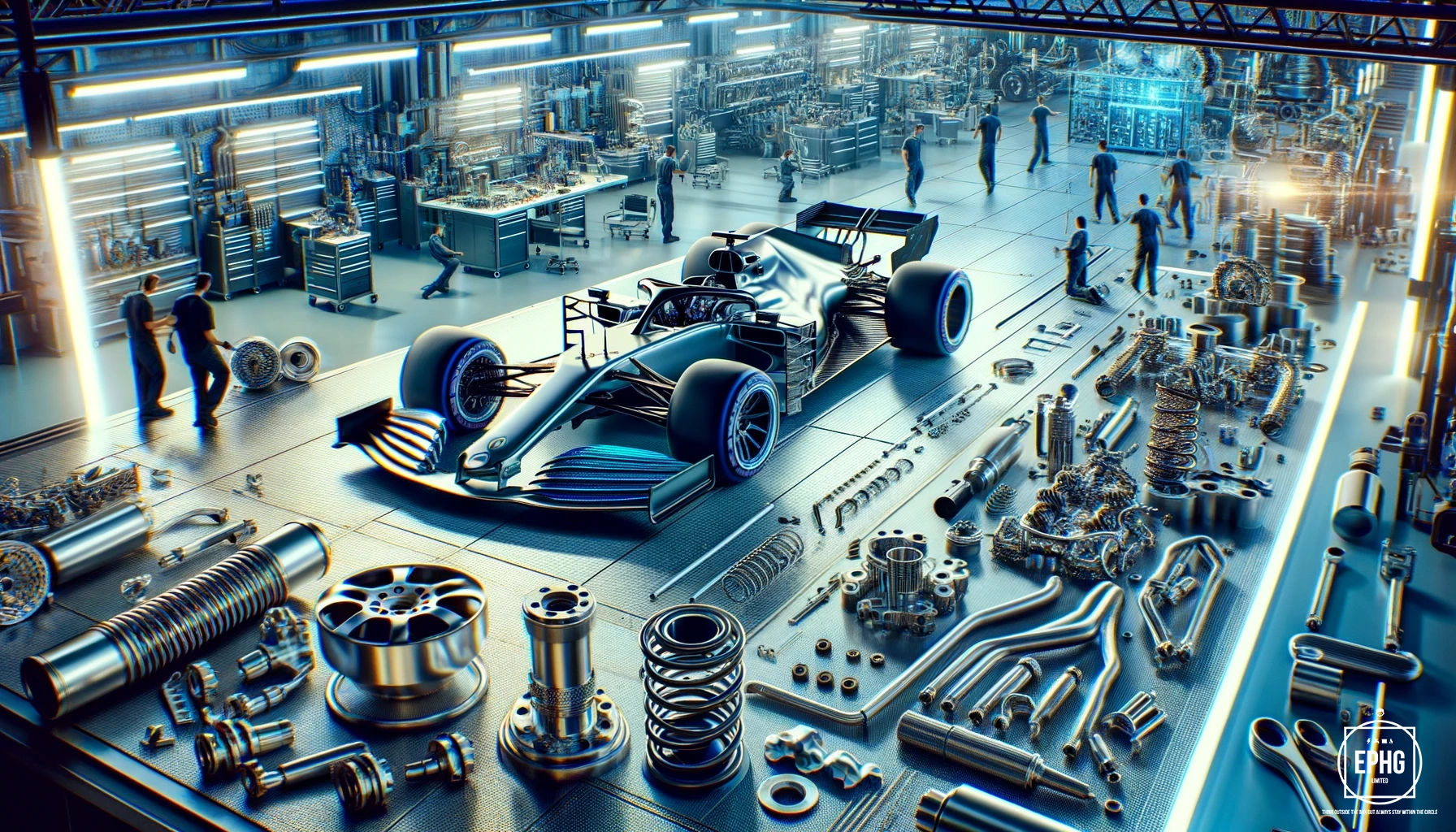
Titanium is increasingly utilized in the automotive sector, especially in high-performance vehicles where every kilogram matters. Key components such as exhaust systems, suspension springs, and critical engine parts are frequently crafted from titanium to significantly reduce weight while simultaneously enhancing performance and fuel efficiency. Motorsport teams extensively use titanium not only to improve speed and agility but also to enhance the overall reliability and durability of their racing vehicles under strenuous conditions. The metal's high strength-to-weight ratio and resistance to high temperatures make it particularly suitable for parts exposed to extreme operational stress.
Consumer Products Made of Titanium
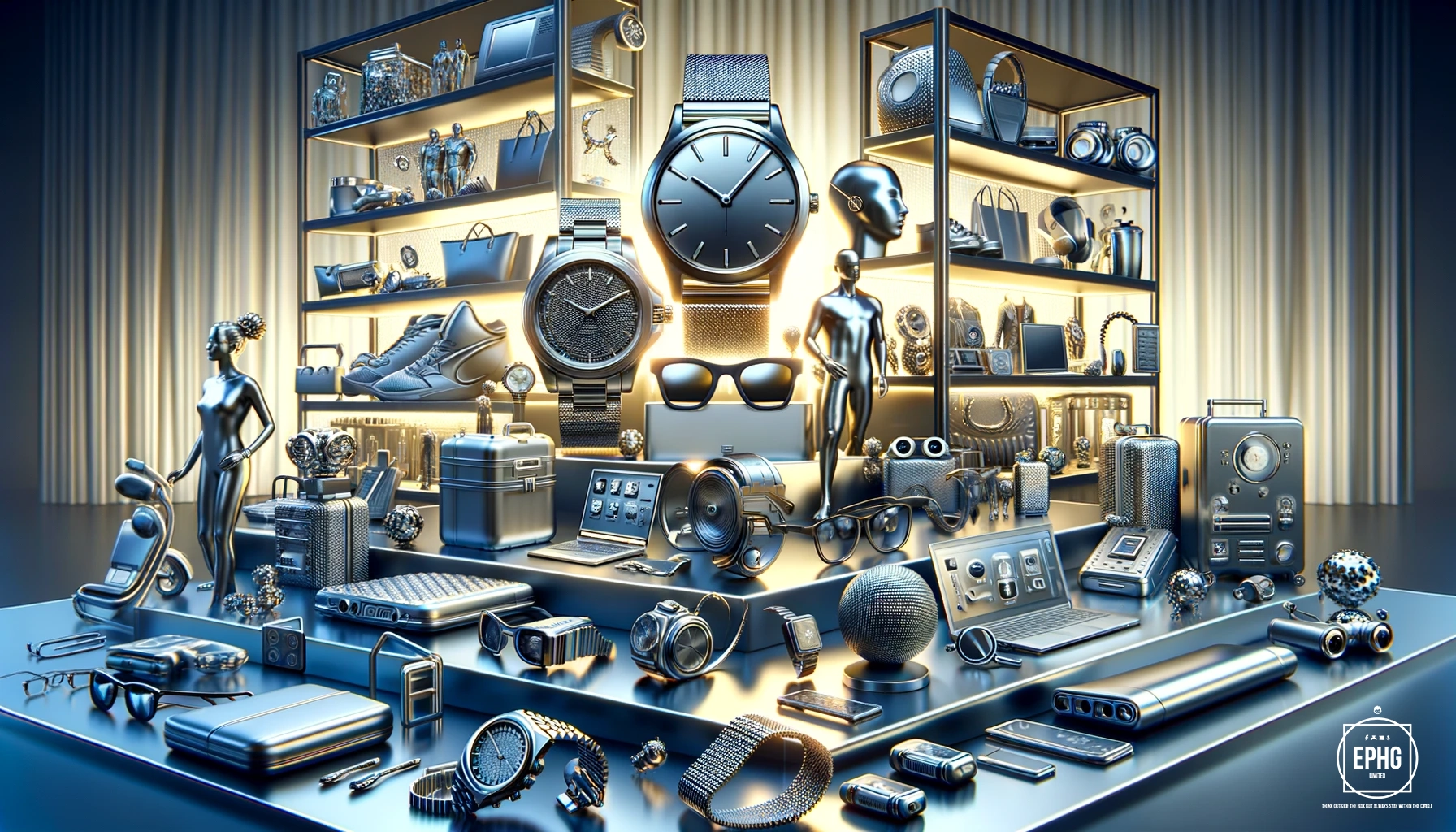
Titanium is increasingly popular in various consumer goods such as eyeglass frames, watches, and sports equipment, prized for its exceptional strength, lightness, and corrosion resistance. These properties make titanium ideal for everyday items that benefit from being lightweight yet durable. Additionally, titanium is used in the manufacturing of laptops and other electronic devices, especially in components that demand thin, robust casings that can withstand daily wear and tear. Beyond these applications, titanium's hypoallergenic properties are leveraged in jewelry and personal accessories, enhancing comfort for users with sensitive skin. Its aesthetic appeal and metallic sheen also add a touch of luxury and style to the products.
Industrial Applications of Titanium
In the chemical industry, titanium’s resistance to corrosive chemicals makes it ideal for manufacturing reactors, heat exchangers, and piping systems. It is also used in the production of paints, pigments, and plastics as titanium dioxide, a white pigment known for its brightness and opacity. In the energy sector, titanium is used in heat exchangers for power plants and as a material for nuclear waste storage.
Military and Defense Applications of Titanium
Titanium's strength, lightness, and durability are crucial for military and defense applications. It is used in armor plating, military aircraft, naval ships, and missiles. Titanium alloys offer high ballistic protection while maintaining relatively low weight, a combination that significantly improves military vehicle performance.
Mining of Titanium in Mines
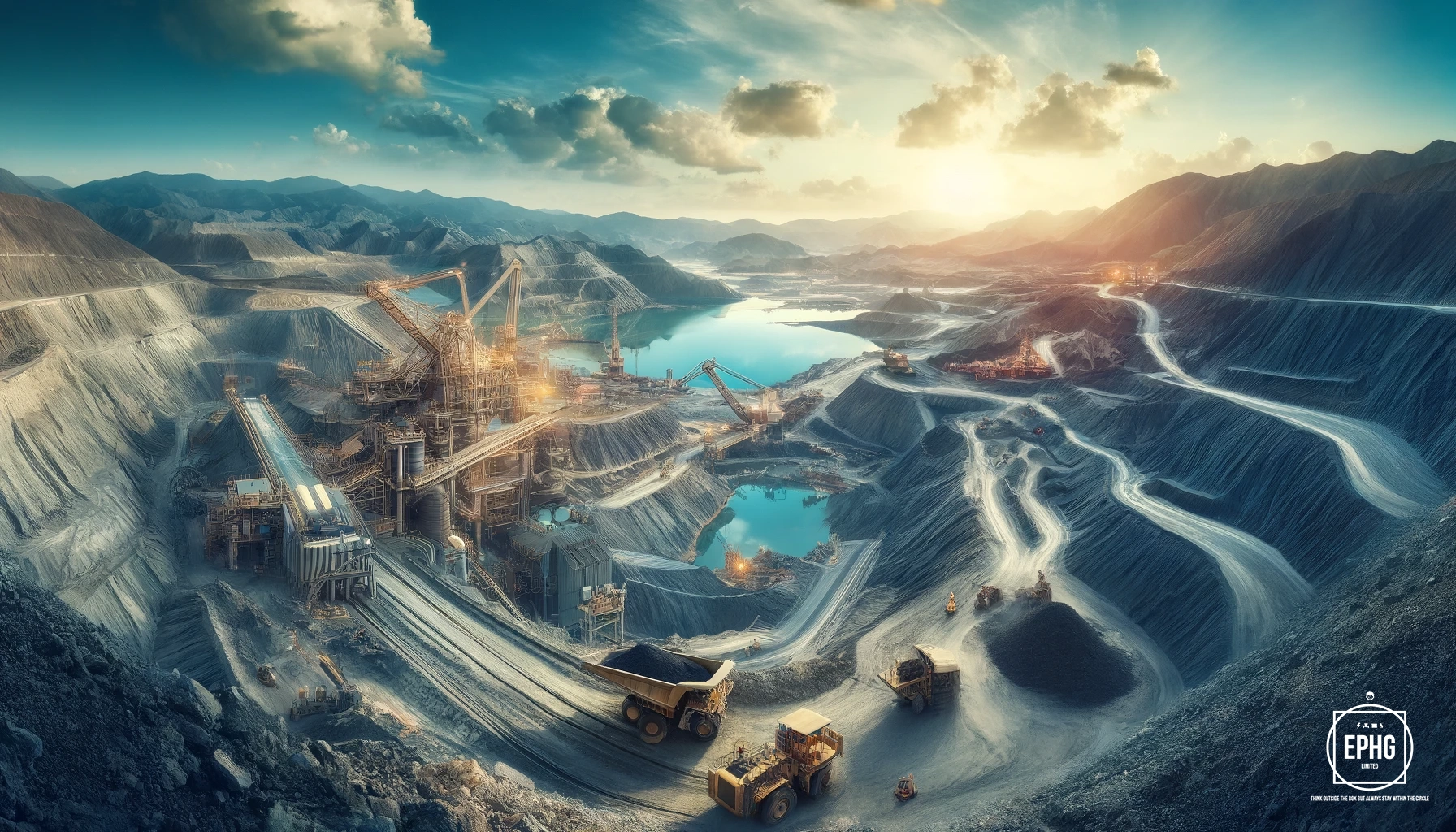
Titanium is primarily extracted from heavy mineral sands that contain a variety of other valuable elements. The mining process involves extracting titanium-bearing minerals such as ilmenite and rutile. These minerals are often found in conjunction with other commercially significant elements. Notably, zirconium, often sourced from the mineral zircon contained in the same ore deposits, and hafnium, which is frequently found in zirconium minerals. These elements are refined through various processes to separate them from titanium and each other, capitalizing on their unique properties for different industrial applications. The extraction and processing of these minerals are critical for the production of not only titanium but also these valuable companion elements that play vital roles in modern technology.
Keeping the memery of Memory of the original name Manaccite, we have dedicated the Moma Mine in Nampula, Mozambque to this name.
Processing and Manufacturing Titanium
Processing titanium into a usable form is a complex task. Its affinity for oxygen and nitrogen at high temperatures makes it challenging to work with. Here are some key steps in the production process:
Extraction of Titanium
Titanium is primarily extracted from minerals like ilmenite and rutile. The Kroll process, developed in the 1940s, remains the primary method for extracting titanium. The process involves reducing titanium tetrachloride (TiCl₄) with magnesium in an inert atmosphere. The resulting metallic titanium is then purified and melted to form ingots.
Refining and Alloying Titanium
After extraction, titanium is melted and refined to remove impurities. It is often alloyed with elements like aluminum, vanadium, and molybdenum to enhance specific properties. The most common titanium alloy is Ti-6Al-4V, which contains 6% aluminum and 4% vanadium and is widely used in aerospace and medical applications.
Forming and Fabrication of Titanium
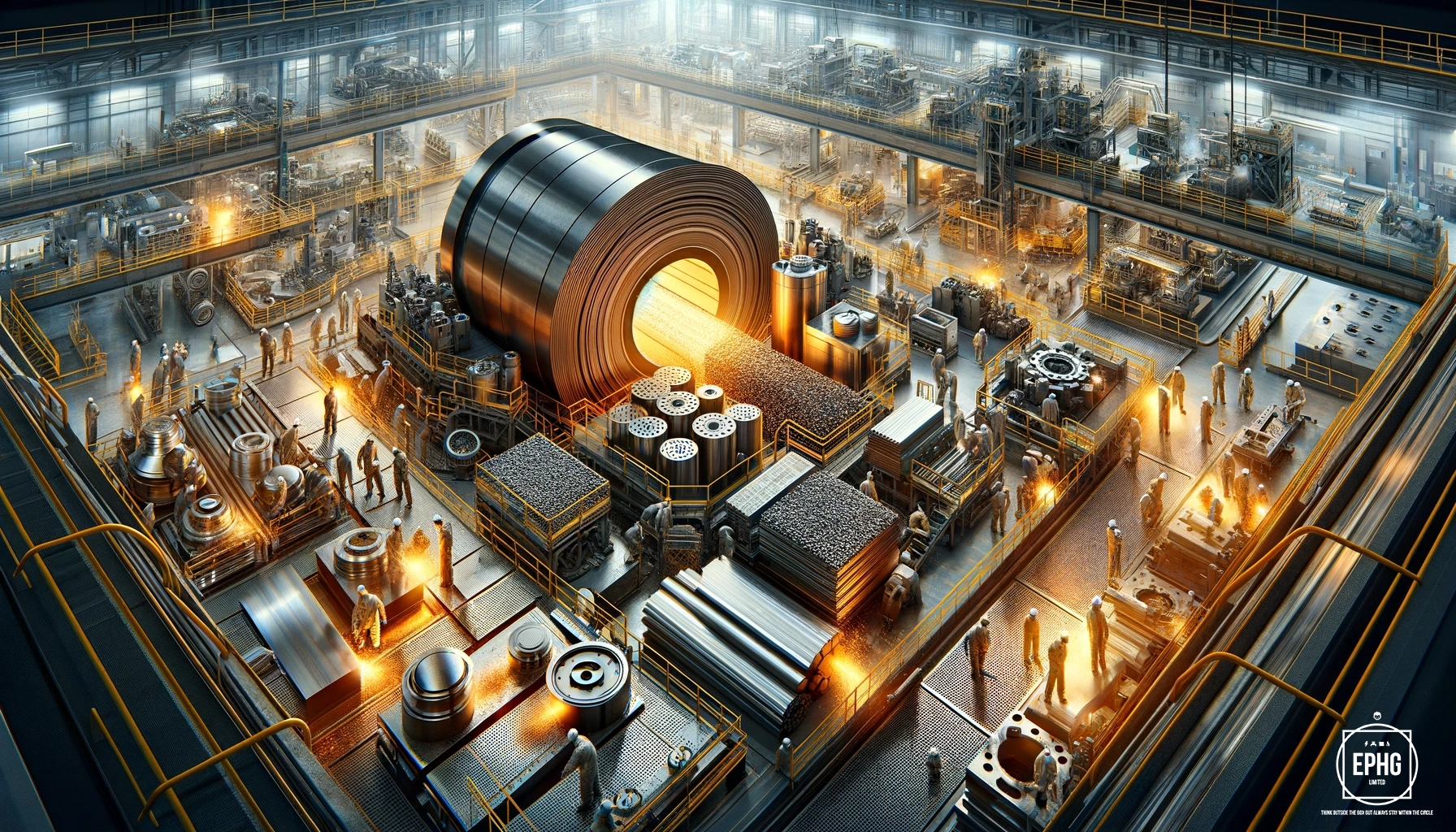
Titanium ingots can be processed using various techniques, including forging, rolling, and casting, each of which prepares the metal for further use in manufacturing. Once formed, titanium can be shaped into sheets, bars, and other structural forms, which are then expertly fabricated into finished products through precise cutting, welding, and machining processes. Welding titanium is particularly challenging and requires an inert atmosphere to prevent contamination; this is often achieved using argon gas or within specialized welding chambers designed to maintain purity. Additionally, advanced techniques like water jet cutting and laser engraving are also employed to handle titanium with the high precision needed for aerospace and medical applications, where even minor imperfections can compromise the material's integrity and functionality.
Challenges and Future of Titanium
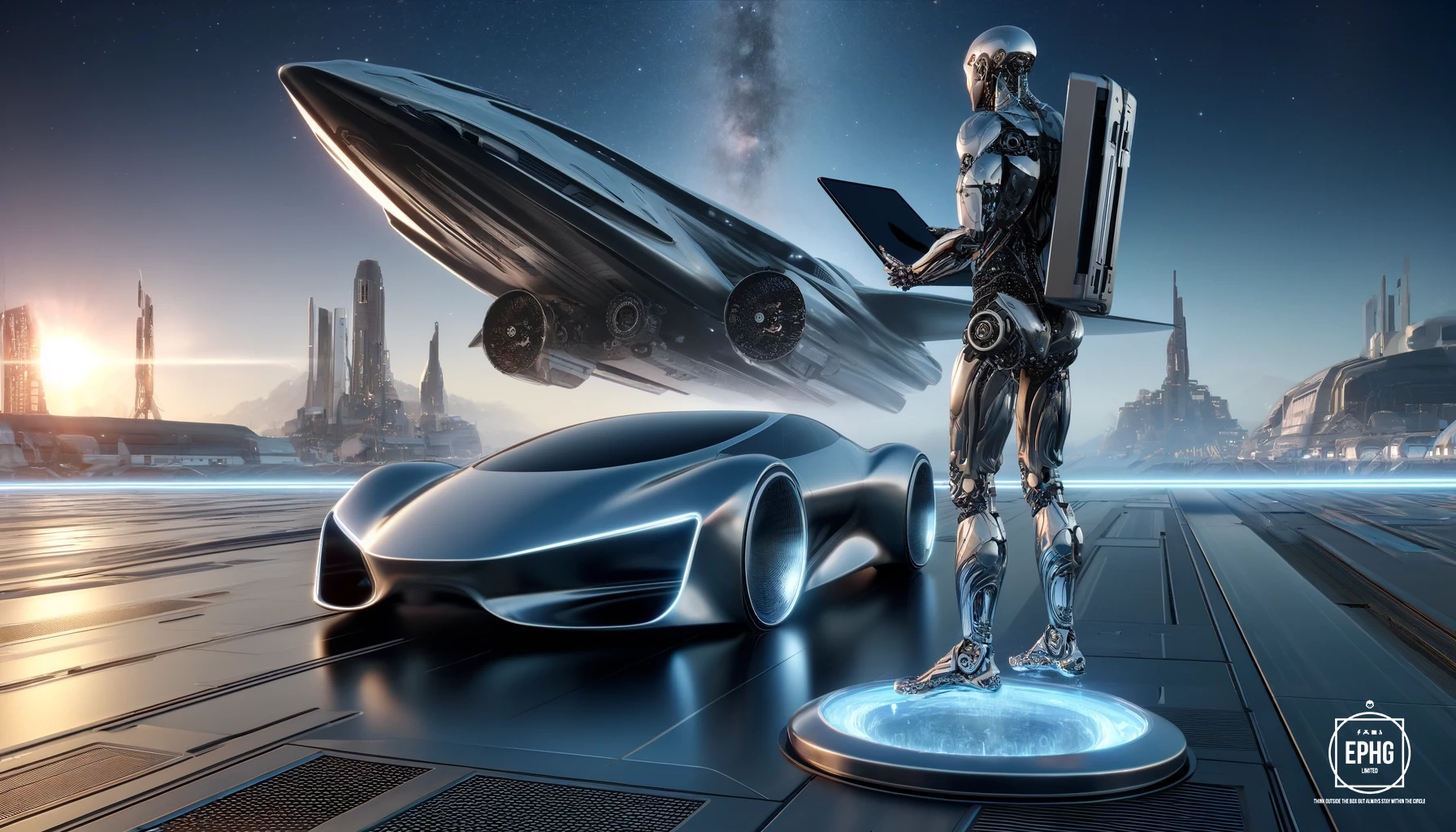
Despite its many advantageous properties, titanium is not without challenges. The cost of extraction, processing, and manufacturing remains relatively high compared to other metals. The Kroll process is energy-intensive and inefficient, leading to high production costs.
Research into alternative extraction methods, such as the FFC Cambridge process, promises to make titanium more accessible. Additionally, advancements in recycling could help lower costs by reusing scrap titanium from manufacturing processes.
In the future, titanium's role in emerging technologies such as electric vehicles, clean energy, and advanced materials will continue to expand. Its potential for innovation in lightweight structures, biomedicine, and aerospace ensures titanium will remain a crucial material in the modern world.